作為一個品質(zhì)管理者,客訴時讓人最讓人頭痛的就是回復改善報告,因為報告回復的好壞代表著一個公司的管理能力和公司形象,可能大家都知道,只要廠內(nèi)出現(xiàn)品質(zhì)問題就要開異常,回報告,不是這報告就那報告的;客戶處出現(xiàn)品質(zhì)問題就更不用說了,現(xiàn)在幾乎所有客戶動不動要回復8D報告,有客戶要求不嚴,隨便回復一下達到一定字數(shù)就行,要求較嚴的客戶那是不行的,必須踏踏實實的分析原因,出一個可行的改善措施的,要不然寫的報告將面臨將一次又一次的退回來,即否定了你的能力,對日后工作也將失出一定的信心,當然也有更狠的客戶,那就是回復不合、超過時限的或達不到求客戶會直接罰款等等情況。
在一個企業(yè)作為一個品質(zhì)管理就有必要了解什么是8D?8D步驟?8D使用?什么情況下使用?
一、先了解決問題時常常會犯下的幾個錯誤。
問題描述不正確,問題描述不夠準確,不夠詳細,令小組不能有效的解決問題;
解決問題過于匆忙,為了得到快速的解決方案,而沒有按照既定的步驟解決問題;
小組成員不能有效的參與或根本就是一個人分析,團隊或個人不能考慮到所有原因;
沒有程序邏輯,沒有系統(tǒng)性的排序,分析,回顧問題;
缺乏專業(yè)技能,小組成員不具備統(tǒng)計和解決問題的方法和能力;
管理層過于焦急,由于管理層對于解決問題的程序缺乏了解,所有的管理層都急需知道問題解決的具體時間,這種壓力導致小組不能準確分析問題。
根本原因識別錯誤,把可能原因快速的識別為根本原因,結束問題調(diào)查,導致并沒有找到真實的原因。沒有執(zhí)行永久糾正措施,可能找到了根本原因;
沒有執(zhí)行永久的糾正措施。長期的行動往往需管理層審批成本并且需要一個閉環(huán)系統(tǒng)。
最常見的錯誤:沒有完全理解和分析就直接從問題跳到答案
二、什么是8D?
8D其它就是簡單的理解就是問題解決法的8大步驟
8D法是改進產(chǎn)品和流程的工具
8D是起源于二戰(zhàn)期間一種類似8D的流程軍事標準,也稱之為不合格品的修正行動及部署系統(tǒng)。從19世紀60至70年代福特汽車公司開始,8D漸漸成為系統(tǒng)性的問題解決方案被普遍使用在品質(zhì)領域以及其他工業(yè)范疇。
8D由8個原則組成,強調(diào)團隊合作。理念是一個團隊比個體的總和更優(yōu)秀更快捷。
三、8D原則是什么(又稱8D步驟)
D0:準備8D程序(下面將會專門介紹)
D1:成立小組:一般就是由相關部門人員組成(如生產(chǎn)、工程、研發(fā)、采購—-)
D2:描述問題
D3:臨時措施又叫:制定過渡性圍堵措施
D4:根本原因
D5:選擇永久糾正措施并驗證有效性(永久改善對策)
D6:實施永久糾正措施并確認結果(糾正措施的驗證)
D7:防止問題再發(fā)生/識別系統(tǒng)性問題(實施預防措施,防止缺陷重復發(fā)生)
D8:表彰小組
四、D0準備工作
1、啟用8D之前需要哪些準備工作?
8D是解決眾多問題的方法之一,在用8D之前,我們要評估此問題是否適合使用此方法;
解決問題前必須執(zhí)行緊急反應計劃保護客戶不受到問題的影響(臨時措施);
量化問題征兆并確認現(xiàn)有的執(zhí)行條件是否有差距;
確定管理層對所需資源是否支持。
2、D0何時適用8D
異常原因不清楚時;
感到異常問題較為復雜性時(一個人不能解決,需要工程、研發(fā)等部門組建成團隊來解決問題);
感到異常有特殊原因特征時;
內(nèi)部程序或工藝發(fā)生變化導致問題時、客戶要求時;
3、D0緊急反應計劃
緊急反應行動是為了防止不良物料繼續(xù)流出并要確保供應鏈不受影響(一般是指出現(xiàn)問題后,應第一時間制定出臨時改善方案,并要及時處理客戶和廠內(nèi)在制品、倉庫成品以及清查在制和貨倉有批次問題的物料,如原因不明,一時沒有結果,應將懷疑有批次的成品或物料進行標識隔離,待結果后再處理)
五、D1組建小組
8D方法強調(diào)團隊合作,好的團隊協(xié)作可以創(chuàng)造比個體更好的效益。小組組成一般由需具備以下條件:
不同部門人員,如生產(chǎn)、工程、品管、研發(fā),一般是先找工程、再找研發(fā),結果再通知相關部門開會一同處理。
具有產(chǎn)品和制程知識,能有分析問題的能力,要合理的安排時間和資源,有相關技術技巧;
能執(zhí)行糾正措施同時要有管理層的支持。
支持者負責統(tǒng)計項目并提供小組所必須的資源和定義項目范圍;
小組人員一般是4-8人(這里最好是單數(shù),如有意見的確定,可舉手表決達成一通過);
小組人員中必須有一個很好組織者,即組長(一般由品質(zhì)部主導);
小組人員中必須有足夠的決策權來確定最后執(zhí)行方案。
六、D2問題描述
問題描述引導著8D程序的方向,可以幫助我們設定并縮小問題的調(diào)查范圍。擁有一個好的問題描述是成功解決問題的一半,是解決問題程序中的一個重要的步驟。
一般按3W1H來描述:
例我們平時一定會碰到這樣的問題,IPQC在反饋問題時會說主管,拉上有很多不良品,您定會問是什么產(chǎn)品,哪條拉上,是什么不良,有多少數(shù)量,此時反饋問題的人一定會再跑到拉上查看,再回來告訴你,又如一個產(chǎn)品有幾個指示燈,其中有一個指示燈不亮,那么在描述時,應準確的描述出具體的哪一個燈不亮,是什么色都要說明,從可知3W1H的意思:
What—-:何事,是事情的內(nèi)容是什么?要抓到問的實質(zhì)性;
where—-:什么地方(何地),是指事情發(fā)生的所在地在哪里?有無轉(zhuǎn)移或變動,是否針對了具體的環(huán)境和當時的狀態(tài);
When—-:什么時候(何時):主要強調(diào)時間因素,事情發(fā)生在什么時間,發(fā)生了多長時間;
How much—-:多少:這里指的是不數(shù)量或不良比例。
D2問題評估:
在解決問題的所有階段中都要考慮客戶:解決問題者和客戶要保持與客戶的溝通,改善的結果與客戶意見保持一致性。
缺陷樣本(不良品)研究分析:因為看實物比看照片獲得的信息更多;
只作觀察:要清楚觀察和最終結論的不同,在這一階段,我們可以用為什么和怎樣的假設,但不要太快達成結論。因為一旦達成結論,大多數(shù)人很難重新審視這問題。
七、D3臨時對策
1、實施臨時對策原因:
正當我們在尋找根本原因和糾正措施時,我們的客戶仍會接觸到和涉及到問題的風險。在這里,我們采取一系列的措施保護客戶利益和返工的成本,隔離有問題的產(chǎn)品并為改善爭取時間。
2、臨時糾正措施界定:
驗證和執(zhí)行臨時糾正措施(ICA)使內(nèi)部和外部顧客都不會受問題影響。
防止問題惡化。
繼續(xù)實行臨時糾正措施,直到永久糾正措施(PCAs)的落實。
驗證臨時糾正措施的成效(效果)。
D3不僅僅是快速改正
暫時的,一旦永久糾正措施準備就緒,臨時糾正措施將會被更換;
基于D2(描述問題)中的數(shù)據(jù)分析展開;
針對影響或具體問題,除了隔離,整理,篩選和測試;臨時糾正措施只針對問題而實施相應的工作;
實施前核查:實施前要核查一下這樣做是否正確。
實施時驗證:實施時必須對產(chǎn)品進行驗證,以免批量改完后又出現(xiàn)問題。
文件化和變更管理:記錄并由權威部門出相應的臨時變更。
D3核查和驗證
核查和驗證往往不能被充分理解。核查和驗證通常一起操作,核查屬之前的證明和驗證屬之后的證明。
核查是對要在某一時間應做和要做的行動的一過確認過程
驗證提供了在某個時間段內(nèi)行動有效的證據(jù)
D3問題評估
在臨時糾正措施選擇時是否知會客戶?
重新制定標準,臨時糾正措施有否提供了最佳的利益,風險和成本平衡?
臨時糾正措施已否被核查和驗證?
我們有否考慮任何可能出錯的機會以及相應備用應急行動
八、D4:識別根本原因和遺漏點
只有糾正根本原因才可徹底消除問題
通過測試每一個可能導致問題的原因和測試數(shù)據(jù)來分離和確認潛在原因的結果。
找出制程中應該可以發(fā)現(xiàn)和控制問題的位置(遺漏點)
分辨過程中問題可能被發(fā)現(xiàn)的控制點
評估目前控制方法的有效性
當多個根本原因被發(fā)現(xiàn)時,該小組應考慮使用另一個獨立的8D
總結一下兩點:
根本原因:包括組件缺陷,在過程或設計或系統(tǒng)故障時發(fā)生的錯誤而導致的不良輸出。
遺漏點:指在過程中未被發(fā)現(xiàn),而之后被客戶發(fā)現(xiàn)的偏差
D4:魚骨圖:主要是通過人、機、物、法、環(huán)找出發(fā)生問題的根本和發(fā)生問題遺漏的根本(就是不良品流出的原因)
魚骨圖主要是利用人、機、料、法、環(huán)、對問題進行分析
利用魚骨圖進行原因分析
D4:5Why:
5Why來源于日本,經(jīng)工程師發(fā)現(xiàn),大多數(shù)根原可由五個為什么找出–因而得其名;
5WHY就是5個為什么,例如:地上有水(這是一個征兆)—為什么在水?原因是人員不小心灑的(潛在原因1)—-為什么不小心?因為水有點燙?(潛在原因2)為什么水燙?因為沒杯拖?(潛在原因3)為什么沒有杯拖?因為杯拖用完了?(潛在原因4)為什么不申請買?因為清潔工請假了(潛在原因5)使問題無法進一步的查詢。
5WHY一直要分析到無法進一步查詢?yōu)橹?/div>
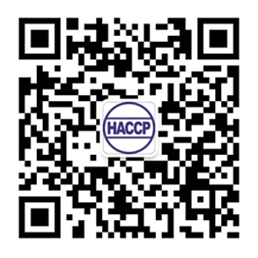
HACCP聯(lián)盟
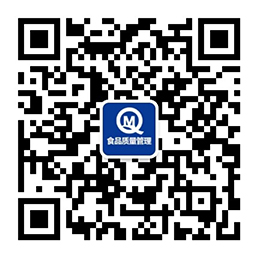
食品質(zhì)量管理
D4解決問題的工具包
收集資料:來源于缺陷映射生產(chǎn)數(shù)據(jù);
原因分析:因果圖,和5WHY;
組織數(shù)據(jù):主要確認問確的是/不是、流程圖、FMEA、控制計劃。
D4問題評估:
1、團隊是否正在解決影響而不是原因?
2、團隊有否太快跳到根本原因而沒有正確認識,分析和核查問題?
3、將問題歸結為操作工而不是全面地看待問題?
4、這是否一個特殊原因造成的問題?如果發(fā)現(xiàn)有多個根本原因,團隊可能正面臨一個普通原因問題,而8D可能不是一個合適的方法來解決此問題。
5、根本原因和遺漏點有否被分辨出來?
6、有否存在一個控制系統(tǒng)以檢出此問題?控制系統(tǒng)有否不同于原始設計?
7、制造過程是否具體檢測出問題的能力?
8、根本原因能否解釋所有在D2中描述編制的事實?
九、D5、選擇和驗證永久措施的有效性
PCA(永久措施)須考慮到所有利益和風險,因此PCA是一個深思熟慮的行動。
行動都不應操之過急,反之可能引發(fā)其他問題或重復發(fā)生。
D5制定永久糾正措施
決定最佳的PCA(永久糾正措施),以消除根本原因和遺漏點。
在實施前,核查這兩個行動的有效性。
確認在永久糾正措施實施后不會有新問題發(fā)生。
PCA的選擇和實施時間表應由客戶批核。
D5防呆措施
最好的解決方案中不可有錯誤。
每當有出錯誤的可能性,防止錯誤解決方案應建立。
質(zhì)量未必能在產(chǎn)品檢測到,它是透過防止錯誤而建立。
D5決定PCA(永久改善措施)
不同根本原因和遺漏點的PCA選擇應分析作解決方案。最佳的PCA選擇應基于團隊的意愿、資源、效益、成本。
考慮到糾正措施所涉及的風險應制定相應的消除計劃
糾正措施必須加以核查,以消除根源問題
團隊成員必須有正確的經(jīng)驗以作出決定
D5PCA的核實
在建立PCA時,其他方案會被一起考慮。
有沒有證據(jù)證明PCA可解決問題根源?
有沒有考慮至核查方法會覆蓋制程和缺陷造成的各種變化?
有沒有把錯誤預防措施放到該解決方案中?
實施PCA的風險有否被評估,減災計劃有否被制定?
PCA的擇所過程中有否涉及客戶?
執(zhí)行PCA的同時,審查計劃以消除ICA(臨時措施)。
十、D6執(zhí)行永久糾正措施和驗證結果:
根據(jù)前階段所做的準備和分析的相關資料8D小組已經(jīng)準備好執(zhí)行已選行動。
D6執(zhí)行和驗證永久糾正措施:
要求廠內(nèi)和客戶一起去驗證永久糾正措施。
廢除臨時糾正措施,驗證永久糾正措施的有效性并建立系統(tǒng)去監(jiān)督長期效果。
D6評估問題:執(zhí)行永久糾正措施
需要什么規(guī)章制度去執(zhí)行永久糾正措施?
需要客戶或供應商如何配合?
是否需要訂立一套行動計劃?職責分配?完成時間的限定?
什么原因容易導致出錯?
做什么可以防止出錯?
考慮適當?shù)膽冃袆樱?/div>
引發(fā)我們的應變行動是什么?
我們?nèi)绾伪O(jiān)察計劃的完成?
什么時候能移除圍堵措施?
將需要怎么樣的培訓?
什么資料(事實與數(shù)據(jù))會用來驗證永久糾正措施的結果?(包括長期和短期的)
D6評估問題:確認永久糾正措施
臨時措施取消了嗎?
不必要的東西已全部移除?
我們怎樣得出結論證明措施可行?
我們?nèi)绾伪O(jiān)督長期效果?
我們以怎樣的衡量標準來監(jiān)控?
客戶的問題100%已經(jīng)解決了?
是否有最好的方法去證明根本原因已消除?
我們?nèi)绾魏涂蛻舸_認效果?
是否所有與問題相關的資料系統(tǒng),作業(yè)習慣,程序文件、BOM等資料都已經(jīng)更新?
十一、D7防止再發(fā)生
到D7后將已解決了系統(tǒng)本身的差距所造成的失效,解決不良問題后,往往有助于提供更全面,更有效的改善行動去防止問題再發(fā)生。
修改必要相關的資料系統(tǒng),作業(yè)習慣,程序文件、BOM、SOP等資料去防止該問題或類似問題再發(fā)生。
在適用的情況下改進系統(tǒng)。
在現(xiàn)有或?qū)淼捻椖恐蟹窒斫?jīng)驗和教訓。
D7有效的系統(tǒng)改進
在處理過程中執(zhí)行GRR和MSA系統(tǒng)。
SPC系統(tǒng)檢測過程的控制。
改善培訓系統(tǒng)。
在處理問題解決過程中要有操作員的加入。
在處理過程中開展和貫穿PDCA系統(tǒng)。
實行預防和預測性維護方案。
從記錄材料中所吸取的經(jīng)驗可用于在后來的新項目中審查和檢驗。制作文件記錄。
解決系統(tǒng)本身的差距,找出可交叉發(fā)展的和標準化的。
D7評估的問題
是什么樣的資料系統(tǒng),作業(yè)習慣,程序文件等原因?qū)е聠栴}發(fā)生或允許不良品流出?需要怎樣改善來避免再發(fā)生?
如何從這此分析過程中從而學習到解決問題,產(chǎn)品開發(fā)和持續(xù)改善行動?
能否標準化?
十二、D8慶祝小組:
團隊和個人的貢獻是被組織認可和值得慶祝的。
項目關閉,完成和總結小組的經(jīng)驗完成8D報告并公布。
認可團隊和個人的貢獻。
慶祝成功。
D8評估問題
保證改善行動已經(jīng)和相關人員溝通OK。
獎勵和認可有關過程的成功。
已為團隊決定適當?shù)莫剟睢?/div>
在改善中好改善方法是否考慮申請獎金和專利?
團隊是否已跨部門重新評估
團隊是否已通過佩恩特圖,柏拉圖,趨勢圖分析下次可能會出現(xiàn)的機會?
我們做為一個品質(zhì)管理者除了解以上的步驟外,在真正的面對客戶投訴時我們要掌握正確處理客戶投訴的方法,同時根據(jù)方法按在上8D方法找出根本原因回復客戶,讓客戶放心,減少返工成本。
編輯:foodqm
分享:
食品伙伴網(wǎng)質(zhì)量服務部為您提供專業(yè)的SC咨詢指導、企業(yè)標準備案、供應商審核、FDA注冊咨詢、ISO9001、ISO22000、HACCP、有機食品認證等服務。
聯(lián)系電話:0531-82360063
電話/微信:15269187106
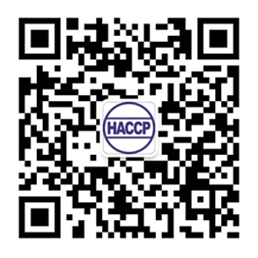
HACCP聯(lián)盟
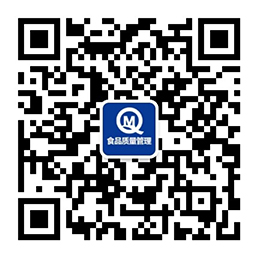
食品質(zhì)量管理
- 下一篇:10條“降本增效”的供應鏈管理法則
- 上一篇:質(zhì)量部崗位與崗位職責大全
推薦圖文
推薦質(zhì)量管理
點擊排行
- CNAS-CC165:2023《HACCP體系認證機構認可方案》
- CNAS-CC185:2023 良好生產(chǎn)規(guī)范(GMP)認證機構認可方案
- ISO 22003-1:2022 食品安全D第1部分:食品安全管理體系審核和認證機構的要求
- BRCGS 包裝材料 (第七版)體系文件清單
- 求ISO 22003-1:2022,《食品安全 D 第1部分:食品安全管理體系審核與認證機構要求...
- 終極版2024年年度培訓計劃
- ISO9001:2015、FSSC22000V6.0、ISO22000:2018、新版HACCP體系四標一體文件清單
- 食品類應急演練記錄
- 新版HACCP手冊
- 公司2022年度培訓計劃,BRC體系中涉及的
- 大公司HACCP體系文件
- ISO22000培訓學習資料
- 重磅分享--BRC最佳實踐指南蟲害控制
- 產(chǎn)品撤回演練記錄
- 消費者投訴管理制度